摘要:针对传统轨迹装车速度慢,货品堆积堵塞,车皮流通量下降,难以满意生产发展的需求,提出了用优化规划技能树立相应的数学模型,对原有的火车快速装车体系液压缸支撑架钢结构进行力学性能核算仿真,使用ANSYS有限元仿真剖析,比较能准确的剖析模型,易把握特性,便于优化规划方案。然后到达合理地散布载荷,保证液压缸支撑架结构安稳,准确剖析其特性,为改善快速装车体系供给了依据。
快速装车体系是一种将散装物料按规则的质量接连的称量并装入列车车厢的体系。其定量装车体系首要有缓冲仓、定量仓以及4个配料闸口和1个卸料闸口组成,而闸口的操控完全由快速装车站内的液压体系所操控驱动,因而快速装车站液压体系就成为快速装车站中最为要害的中心设备,被誉为快速装车站的四肢和肌肉。因为液压缸支撑架在开关闸口时遭到了很大的冲击载荷,如何能保证液压缸的安稳作业,关于快速装车体系好坏有着决议性的效果。所以对液压缸支撑架的力学剖析,关于改进快速装车体系有着至关重要的含义。
1 火车快装体系液压缸支撑架模型树立
火车快装体系液压缸支撑架是由型钢组成的钢结构,上下为H型钢,左右为C型钢,余下为钢板。长度为3 m,宽为0.32 m。
1.1 所选用资料的参数
资料选用Q235-A钢,其资料参数为:
1)杨氏模量E=200 000 MPa;2)泊松比μ=0·3;3)密度ρ=7·8 x 10-6 kg/mm3。
1.2 模型网格区分
因为模型多个别组成一个全体模型,选用自在网格对其进行区分。自在网格是主动化程序最高的区分技能之一,它能够在面上(平面、曲面)主动生成三角形或四边形网格,在体上主动生成四面体网格。通常状况下,可使用ANSYS的智能尺度操控技能(SMARTSIZE指令)来主动操控网格的巨细和疏密散布,也能够人工进行设置网格的巨细并操控疏密散布,以及挑选分网算法(MOPT指令)。关于较杂乱的模型而言,这种区分法省时省力,确认是单元数量通常会很大,核算功率下降。一起,这种办法关于较杂乱的三维模型只能生成四面体单元,为了取得较好的精度,主张选用二次四面体单元(solid92),本文选用solid92单元对模型进行网格区分。
1.3 载荷的确认
本文是以闸口最大接受压力150 t为例,物料与闸口板之间的摩察系数为0.3,所以每块闸口板所接受液压缸给的最大驱动力由公式:
F=μN. (1)
所以得出F=4.5×106N,即每块闸口板遭到驱动力为2.25×106N。
跟着闸口板越开越大,跟着物料的下落,其所遭到的压力就会越来越小。液压缸驱动力是一个改变的进程,关于快速定量装车站要求,一般要求在455 s内完结一节车厢的装车,而且每两节车厢之间有105 s的换车时刻距离,一节车厢的实践装车时刻只要30 s。体系要求单节车厢装载精度差错小于0.3%,为保证高速卸料的准确操控,液压闸口的启闭速度就十分要害,而体系流量决议了油缸运转速度,而一切执行机构中配料闸口的封闭速度及其流量剖析则是保证装车精度的要害。经过一个循环的配料时刻分配(快速
配料3 s,中速配料2 s,精密配料4 s),取2 s是体系流量最大,即驱动力最大。依据F随时刻改变设方程为:
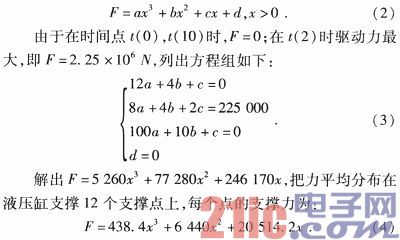
闸口板上跟着闸口的翻开的进程中,面积的减小与物料的削减,压力不断的减小。此进程可当作一个线性进程,在闸口翻开的瞬间,每块板的最大压力为F=7.5×106N,均匀散布在每板20个支撑点上F=3.75×105,设方程为:
F=ax+b. (5)
依据在t(0)时,F为最大值;t(10)时,F=0解得:F=37 500-3750xx,x>0。
2 试验成果
依据以上所界说的弹性模量、泊松比以及对自在度的束缚和载荷的增加,在ANSYS剖析成果,剖析GUI指令为:Main Menu>Solution>Solve>Current LS,当弹出Solution is done的提示框后,表明模型剖析结束,就能够经过后处理器检查模型剖析成果了。如下面的图所示,模型的各个位移改变、应力改变、应变改变等等。所选用的单位制为:m—s—kg—N—kPa,后文各图如无注明单位,均遵从此单位制。
如下图1到4,为液压缸支撑架在有限元力学性能剖析前后的模型位移比照,由图可知其首要变形的方位在于与液压缸支撑点衔接的固定板以及液压缸的支撑点。
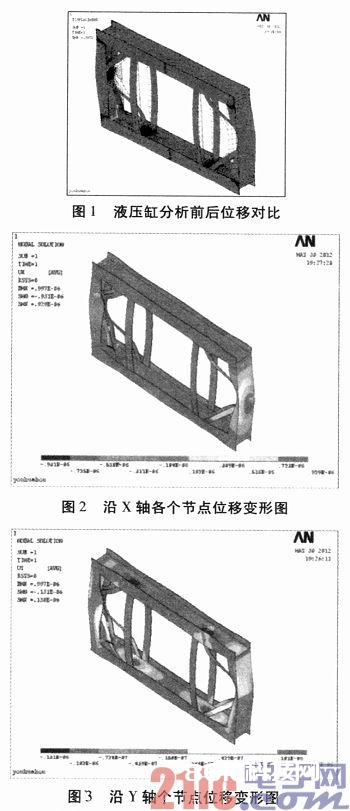
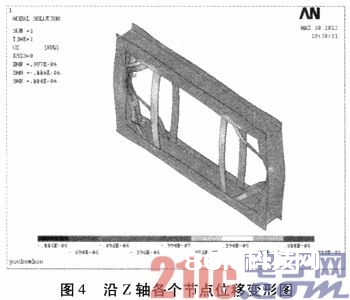
由图1至图4得出沿X,Z轴位移最大的点在液压缸支撑点邻近分别为节点10 176,位移为0.927 67×10-3mm和节点31 400,位移为0.842 87×10-3mm;沿Y轴最大的位移点在固定板与上下H型钢的衔接处为节点352 726,位移为0.129 61×10-3mm。

由图5能够看出,各个整个模型应力散布的状况,沿X轴应力散布首要会集在于10.6 MPa至15.248MPa这个范围内;沿Y轴应力大部分首要会集在5.621 8 MPa范围内,但是在液压缸支撑点,还有支撑板与其的衔接处、支撑板与H型钢衔接处应力散布高达16.869 4 MPa;沿Z轴应力首要会集在9.01 MPa至10.4 MPa范围内。
单个液压缸的最大载荷为2.25×106 N,挑选的液压缸参数为下表所示:
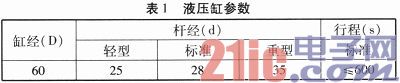
依据最大载荷核算出油缸的最大作业压力:

从上面剖析模型的应力,有些方位最大应力超过了液压缸最大作业压力,会导致体系的不安稳性,影响体系作业的作业状况,为此,需求对此模型进行优化,合理地散布载荷,保证液压缸支撑架结构安稳、牢靠的作业。